やさしいあかり グリーン照明 LED
第6回:LEDの製造工程(3)~チップパターン形成工程~
JR東日本は、山手線の車両内の照明にLEDを導入するための実証実験を行うと発表しました。実験は数年間にわたって行われ、他の在来線にも広げていく予定です。蛍光灯に比べて消費電力を4割削減でき、CO2排出量も年間12トン減らせる見込みといいます。今回もLEDについてわかりやすく解説します。前回のエピタキシャル結晶成長工程に続き、チップパターン形成工程についてです。
チップパターン形成工程
前回に説明した発光層の上に、パターン形成工程では、電極や保護膜などを形成し、図1のようなLEDチップに仕上げていきます。ここではオーソドックスなGaAS基板のパターン工程を素子分離溝、透明電極(p型電極)、パッド電極(n/p型)、保護膜の順に説明します。まず、ウェーハ裏面を研磨して基板を除去します。その後、素子を分離するための溝の形成にフォトリソグラフィ技術を利用します。レジストと露光装置を用い、分離する部分を選択し、マスクがない部分(p型GaN層と発光層、n型GaN層)をドライエッチング装置を用いて除去。素子に溝を作ります(図2)。
図1:パターン形成されたLEDチップ
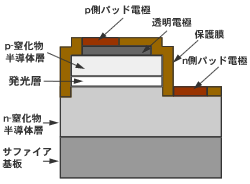
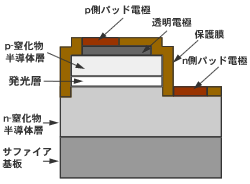
図2:素子分離溝の形成
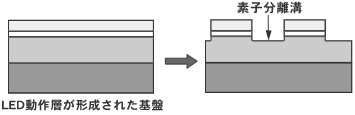
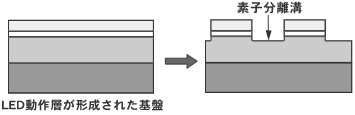
P型電極となる透明電極をフォトリソ技術で形成し、電極材料を真空蒸着で成膜します(図3)。電極に利用する材料はAu(金)を含んだ合金です。レジストと余分な電極を剥がすリフトオフ加工により、フォトリソで選択したエリアが凹み電極ができます。PN接合で発光した光はこの透明電極を通して外部に出ていきます。
パッド電極もフォトリソで形成します(図4)。エッチングして剥き出しになったn型GaN層と透明電極のp型電極材料にマスクをつけて金属材料を蒸着で成膜します。その後は再度リフトオフ加工でレジストと電極材料を取り除いてパッド電極が完成します。
保護膜はCVD法により全体に形成します(図5)。その後、フォトリソでn型のパッド電極とp型の透明電極部分を選択・除去します。 成膜後、結晶層の半分をカットするため、裏面をワックスで固定し、表面をレジストで覆い金属電極の剥離を防ぎます。以降は、基板で一括処理していた工程から1つ1つの素子に分離していく工程になります。まず、水をかけながらダイヤモンドカッターで溝を入れ、表面処理を行った後、レジストを溶剤で取り除き、基板を固定していたワックスを溶かして貼りつけていた板から剥がします。
図3:透明電極の形成
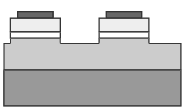
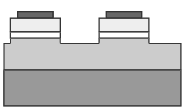
図4:パッド電極の形成
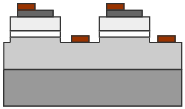
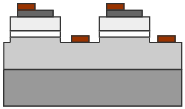
図5:保護膜の形成
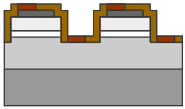
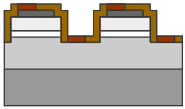
完成後の検査工程では、波長を測定しLEDを選別します。輝度も測定して、ランク分けしていきます。その後、シートを貼りつけ、半分まで切れ込みの入った基板をスクライブ&ブレーキングしてチップ形状にします。最後の外観検査を通過したものがLEDチップとして出荷されていきます。
LEDはまだ新しいデバイスのため、これまで紹介してきたプロセスがベストという訳ではありません。日々刻々と進化しています。新たな製造技術の提案が次々とされています。これまで、半導体製造と重複するプロセスは、装置に何らかの改良を加えることで効率的な製造ができましたが、LED特有のプロセスは未だに手作業で行われているというのが実情のようです。
LEDのダイシングを展開する装置メーカーのディスコは、青色LEDなどに用いられるサファイア基板の薄型化の新加工プロセスを提案しています。サファイア基板は、従来のワックス固定によるLEDプロセスでは反りが激しく、加工しづらいのが課題でした。そこで、リングフレームとテープで基板を固定してグラインディング、ポリッシングを行うというものです。これにより、加工品質の改善に加え、ワックス固定、加熱・剥離の貼り替え 、洗浄などの工程が削減できる他、同一のテープフレームで加工できる特徴をアピールしています。
[上原清志,LEDLED]